What is Lean?
Lean? That’s just the latest fad isn’t it?
Lean has been around for about 80 years. It is now the world’s predominant quality practice in all sectors because it is so effective at invigorating organizations and people’s working lives through a laser-focus on value for clients
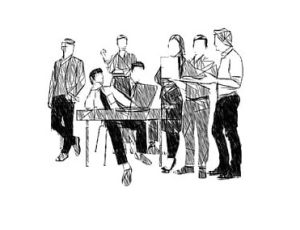
Starting with A definition of Lean
Lean is gaining popularity over decades because it offers “more for less” – meaning more value for your end users and less cost to you, in terms of money, time and effort.
That’s because Lean is defined as the beating heart of an organization where you concentrate on maximizing value to end users and cutting out waste activities in a professional and disciplined way, using the principles and tools presented on this website.
A Lean approach means understanding where you really create value in your workplace (the Gemba), and then removing any activities that do not add value for end users.
And that is markedly different from standard quality systems where the emphasis is on making processes more effective and efficient.
But it all started with Jidoka…
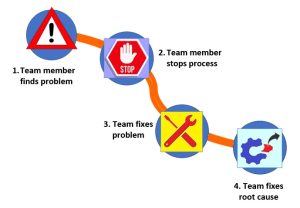
What is Jidoka?
Jidoka is one of the most important Lean methods for ensuring problems – waste – never pass to the next step in a process.
Initially, Jidoka applied to solving mechanical problems at Toyota. But its success led to applying Jidoka to the workforce: managers insist that a team member stops a process if they discover a problem.
But we don’t just stop the process – we highlight the problem, all of the team works to correct it and then we tackle the root cause to prevent the problem ever happening again.
The beneficial side effects are the multi-skilling of the workforce and continually improving workplace processes.
That leads to the “Toyota House of Quality“…
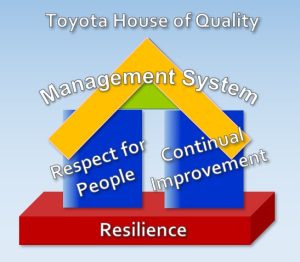
What is the Toyota House of Quality?
Moving forward from Jidoka, where team members support each other to resolve problems, the question was asked again and again: “What are the fundamental elements of a system to get people thinking and working together effectively?“
Toyota used the Jidoka theme to answer this question by a simple system that has the two pillars of Lean quality:
Respect for people – the principle that every team member should be actively engaged in their own development as well as the design and running of their own workplace. The belief in teamwork and respect using Kaizen (small-step improvement) is key to making Lean work.
Wisdom and Continual Improvement – once respect is established, team members feel able to contribute to Kaizen – small step improvement in workplace processes. By grasping the principles of Lean and being adaptable, you understand the current situation in your workplace and use disciplined steps to achieve future objectives.
Info Box
Explore the 5 Lean Principles
Womack and Jones published a book: Lean Thinking which introduced “a proven path of learning to work together more effectively”. Learn about their 5 Lean principles.
Start with Lean techniques now
Click here to change this text. Lorem ipsum dolor sit amet, consectetur adipiscing elit. Ut elit tellus, luctus nec ullamcorper mattis, pulvinar dapibus leo.
Handle problems using Lean
Click here to change this text. Lorem ipsum dolor sit amet, consectetur adipiscing elit. Ut elit tellus, luctus nec ullamcorper mattis, pulvinar dapibus leo.